Recupero del refrigerante
Prova di tenuta
Vuoto all’impianto
Riempimento dell’impianto
Messa in funzione
PROCEDURA
- Montare la batteria manometri
- Aspirare refrigerante nel ricevitore di liquido
- (pump-down nel serbatoio se possibile)
- Spegnere l’impianto (togliere corrente, ma non alle resistenze carter)
- ATTENZIONE: con pompe di calore o recupero del calore:
scaricare o mettere in circolazione il circuito idraulico per evitare congelazioni dell’acqua - Collegare la stazione di recupero
- Collegare la bombola di refrigerante vuota sulla bilancia
- Recuperare il refrigerante dall’impianto
- ATTENZIONE: bombola riempita massimo al 75%
- Arrestare il processo di recupero quando nell’impianto ci sono 0,2 bar(rel)
- Attendere che la pressione salga nuovamente
- Ricominciare il recupero fino a 0,2 bar (eseguirlo le volte necessarie)
- Recuperare tutto il refrigerante
STAZIONE DI RECUPERO
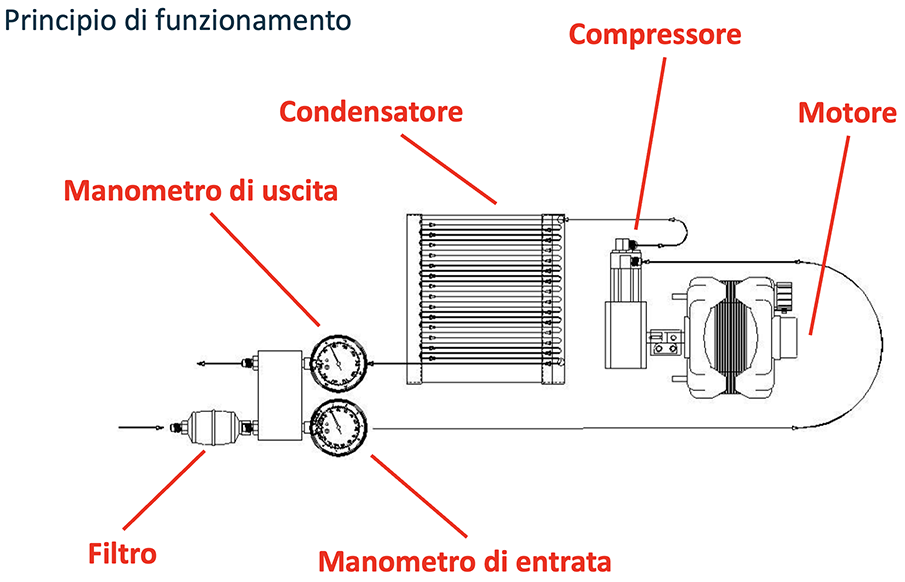

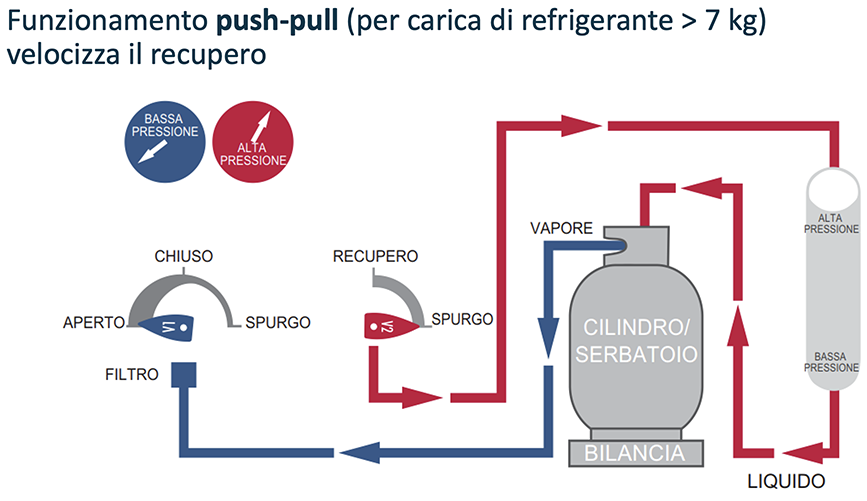
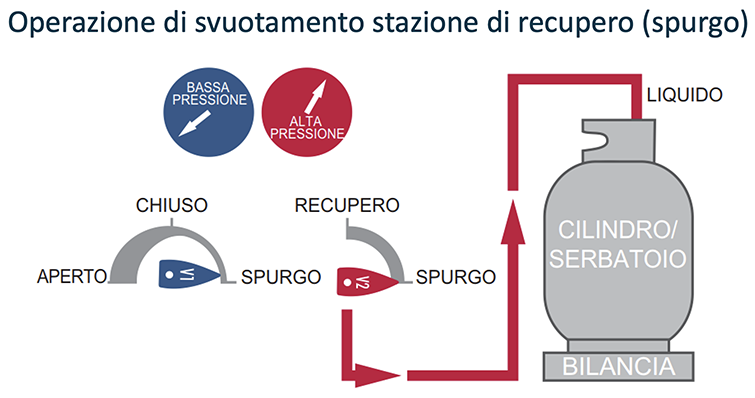
La definizione «ERMETICAMENTE CHIUSI» presuppone secondo la norma SN EN 378-1:2017 paragrafo 3.1.7 quanto segue:
- tutte le parti contenenti prodotti refrigeranti sono saldate, brasate o ermeticamente assemblate con un giunto equivalente non amovibile;
- l’impianto contiene valvole e attacchi di servizio con tappi che consentono un’adeguata riparazione o smaltimento;
- a una pressione inferiore di almeno un quarto da quella massima consentita, l’impianto presenta un tasso accertato di perdite inferiore a 3 grammi l’anno.
Pertanto, prima della carica si fa una prova in pressione con azoto per identificare eventuali grosse perdite.
Dopo la carica del refrigerante si esegue una prova più raffinata col cercafughe elettronico, per assicurarsi di non avere perdite d’entità maggiore a 3 g/anno.
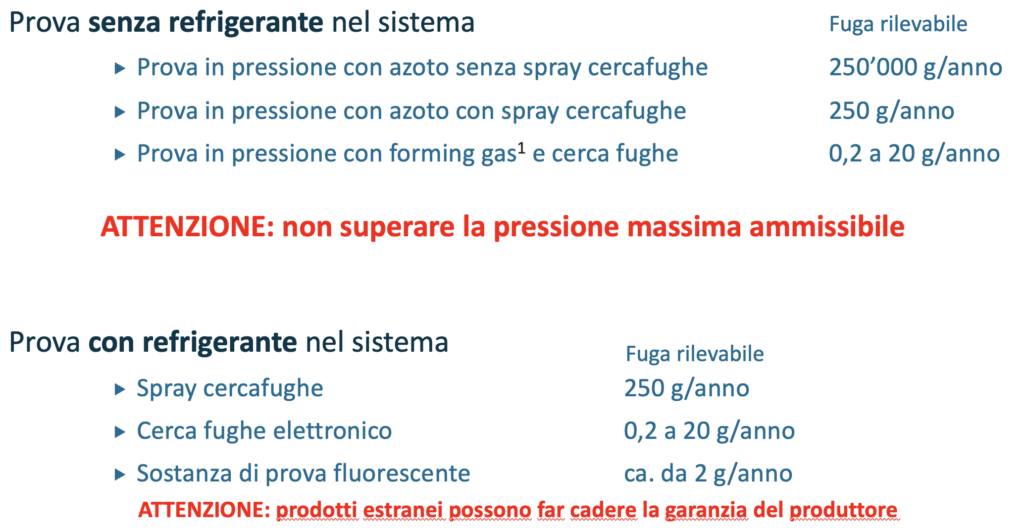
PROVA DI TENUTA CON AZOTO
- NON superare la pressione massima ammissibile
- verificare la taratura della valvola di sicurezza
- aprire tutte le valvole di regolazione e/o solenoidi presenti
una variazione della Temperatura importante comporta una variazione della pressione
p1 / T1 = p2 / T2
p1 pressione assoluta iniziale (pressione manometro + 1 bar)
T1 temperatura assoluta iniziale (T[°C] +273)
p2 pressione assoluta finale (pressione manometro + 1 bar)
T2 temperatura assoluta finale (T[°C] +273
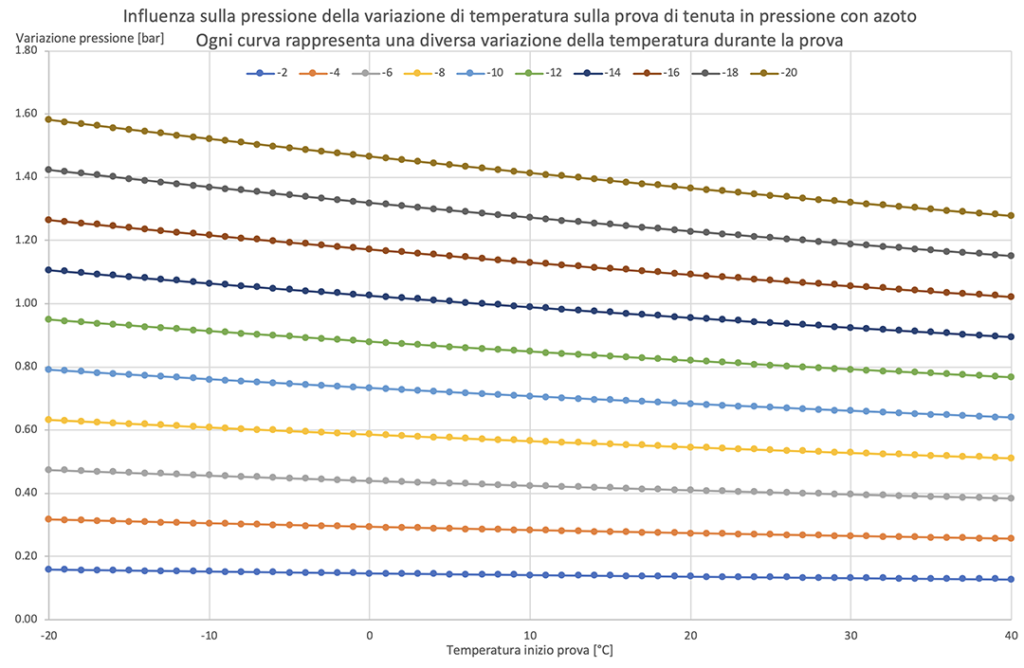
PROCEDURA
- Aprire tutte le valvole di regolazione e/o solenoidi presenti
- Prova di tenuta con azoto (se non c’è refrigerante nell’impianto)
- Riscaldare la pompa del vuoto (accenderla e farla girare)
- Eseguire il vuoto
- Rompere il vuoto con azoto (azoto assorbe umidità)
e se necessario sostituire il filtro - Eseguire il vuoto (0,25 mbar = 200 micron)
- Prova di tenuta in vuoto
- Caricare il refrigerante
SCOPO
- Rimuovere aria e gas estranei
- Evaporare l’acqua per depressione
- e rimuovere l’umidità residua
Pressione da raggiungere sicuramente inferiore alla pressione di evaporazione dell’acqua alla temperatura ambiente.
(in estate sarà più semplice rimuovere l’umidità)
Il vacuometro deve essere montato
il più lontano possibile dalla pompa del vuoto!
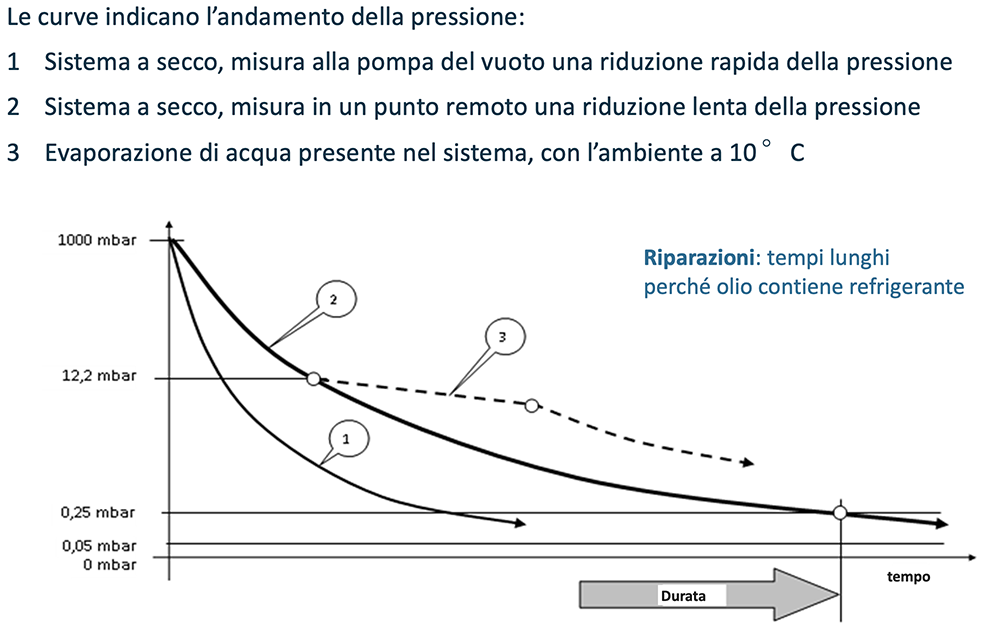
VUOTO DA RAGGIUNGERE
Vuoto spinto, ossia, inferiore a 400 Micron (< 0,5 mbar)
non è necessaria nessuna rottura del vuoto
con impianto nuovo si dovrebbe raggiungere i 200 Micron (< 0,25 mbar)
Vuoto da 400 a 2000 Micron (0,5…2,6 mbar)
è necessaria almeno 1 rottura del vuoto
Vuoto sopra i 2000 Micron (> 2,6 mbar)
sono necessarie almeno 2 rotture del vuoto
400 Micron
= 400 μmHg (micro metri di colonna di mercurio)
= 0,4 Torr = 0,4 mmHg (millimetri di mercurio)
Torr sta per Torricelli, inventore del barometro a mercurio
1 bar = 760 Torr = 760 mmHg
ROTTURA DEL VUOTO
1° Metodo
- caricare azoto nell’impianto fino ad avere ca. 0,5 bar(g) nell’impianto
- sfogare la pressione in eccesso riducendola fino a 0,1…0,2 bar(g)
(in questo modo una buona parte dell’umidità esce con l’azoto) - fare nuovamente il vuoto
2° Metodo
- flussare azoto nell’impianto sfogandolo dalle fruste sul manometro prima in un senso e poi nell’altro, così che con l’azoto esca anche l’umidità evaporata col vuoto precedentemente eseguito e che l’azoto assorbe
- fare nuovamente il vuoto
Utilizzare azoto deidratato (secco)!
POMPA A PALETTE BISTADIO
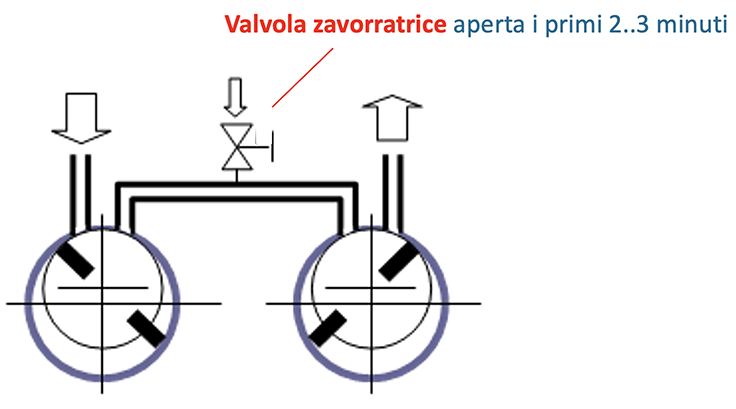
La valvola zavorratrice si apre ad inizio procedura per evitare che la grande quantità di umidità estratta vada ad impregnare l’olio, degradandolo velocemente.
Cambio olio consigliato ogni 15..20 ore di funzionamento
(per sistemi fortemente sporchi o se umidi, più frequentemente)
DURATA DELLA MESSA IN VUOTO
Dipende da:
- volume impianto
- umidita nell’impianto
- temperatura ambiente
- quantità di dispositivi di regolazione della portata (strozzature) presenti
- capacità della pompa del vuoto
- perdita di carico del tubo di collegamento e relativa rubinetteria
- presente tra la pompa del vuoto all’impianto
(utilizzare un tubo di collegamento corto e di grande diametro
meglio se è un tubo di rame e non una frusta che può non essere ermetica)
Per un impianto standard piccolo il tempo minimo è di almeno 30 minuti dall’ultima rottura del vuoto!
PROCEDURA
- Avere un’idea della carica necessaria
- Collegare le fruste
- Scaricare le fruste mediante pompa vuoto
- Mettere la bombola sulla bilancia e fare la tara (azzerare)
- Riempimento (in fase liquida o gassosa a seconda del refrigerante)
- Avviare il sistema
- Continuare col riempimento fino ad aver caricato la giusta quantità
(specifiche del produttore o carica del serbatoio)
ATTENZIONE: la carica varia a seconda del periodo (estate/inverno) - Chiudere la bombola e aspirare dalla frusta di BP
VUOTO DA RAGGIUNGERE
Rompere il vuoto con refrigerante gassoso:
rompere il vuoto con del refrigerante liquido creerebbe abbassamenti importanti e repentini della temepratura col rischio di fissurazioni
raggiunti 0°C è possibile caricare in liquido
scambiatori ad acqua attenzione a non scendere sotto zero
Riempimento delle miscele R400 e R500 sempre in forma liquida (R410A, R449A, R407C, etc.) Gli altri refrigerantipossono essere caricati in forma gassosa o liquida (R134a, R744, etc.)
PROCEDURA
- Collegamento della batteria manometri
- Regolare pressostati
- Misurare le pressioni e le temperature
- Valutare le misurazioni e, se necessario, intervenire
- Impostare i regolatori di pressione (se disponibili)
- Compilare il protocollo di messa in funzione
- Controllo di tenuta con cercafughe elettronico
- Redigere il libretto di manutenzione (obbligatorio da 3 kg di refrigerante)
- Staccare la batteria manometri
- Chiudere gli schrader con tappi (non i tappi a mano)
- Controllo perdite dove si sono scollegati i manometri
- Pulizia dell’impianto
- Notifica impianto (obbligatorio da 3 kg di refrigerante)
REGOLAZIONE PRESSOSTATI
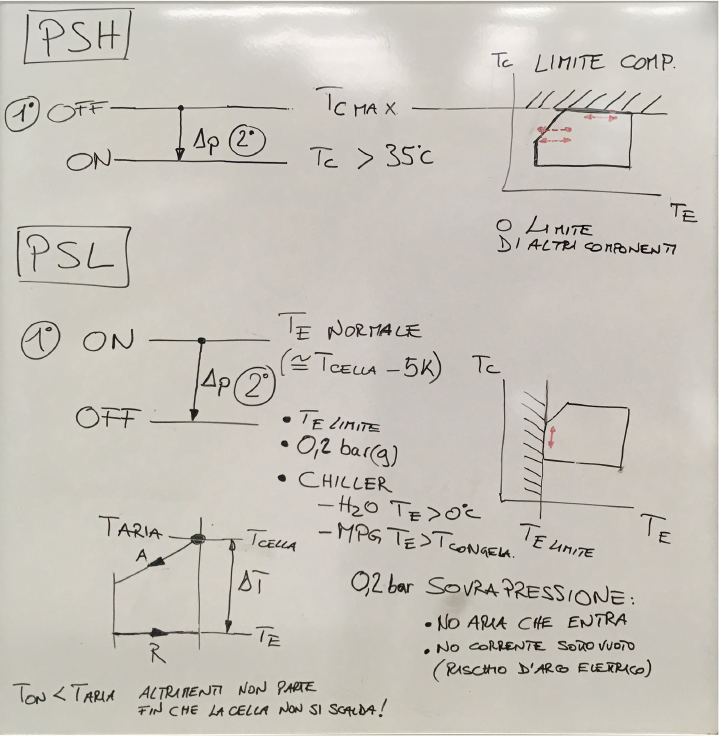
Regolazione PSH (alta pressione)
- 1° componente più debole
- 2° limite compressore
- 3° contesto di utilizzo
Regolazione pressostati in funzione al contesto di utilizzo:
PSH cella o chiller non andare al limite (es. 55°C)
45°C bastano perché la resa resti accettabile.
Regolazione PSL con compressori SCROLL
Spegnendo uno scroll in pump down, la bassa pressione si rialza per la riespansione del gas in alta pressione.
fermando a 0,2 bar(g) la pressione risale anche di 0,5…1 bar
La partenza deve essere regolata ad una pressione maggiore
della pressione presente dopo l’arresto!
Altrimenti si avrebbe un eccesso di avviamenti e compressori che durano poc
VALORI DA MISURARE
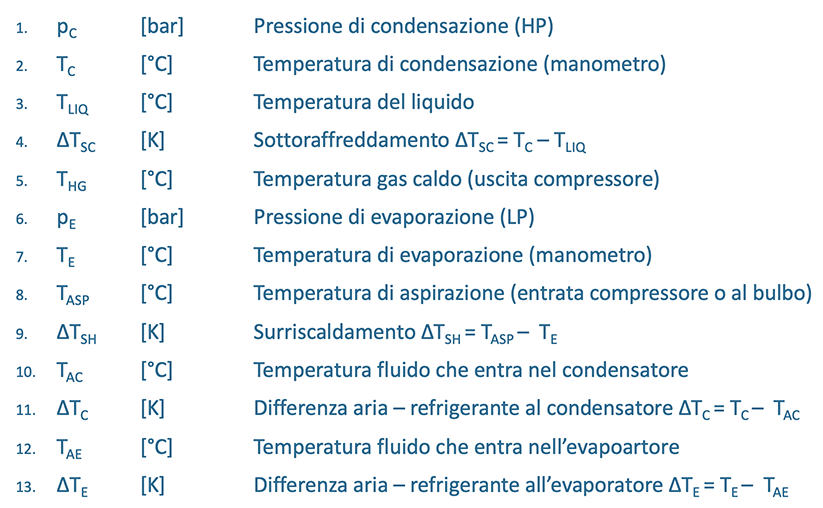
ATTACCHI PER LE MISURE
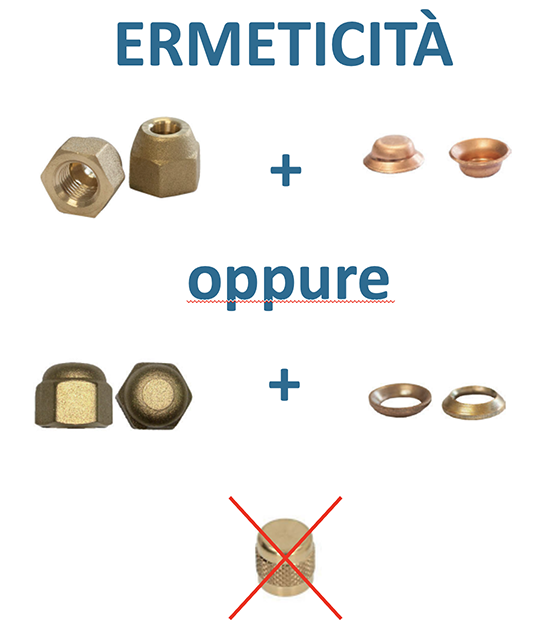